Partes O Elementos Que Componen El Torno Paralelo
Bancada:
Sirve de soporte para las otras unidades del torno. En su parte superior lleva unas guías por las que se desplaza el cabezal móvil o contrapunto y el carro principal.
Cabezal fijo:
Contiene los engranajes o poleas que impulsan la pieza de trabajo y las unidades de avance. Incluye el motor, el husillo, el selector de velocidad, el selector de unidad de avance y el selector de sentido de avance. Además sirve para soporte y rotación de la pieza de trabajo que se apoya en el husillo.

Cabezal Móvil:
El contrapunto puede moverse y fijarse en diversas posiciones a lo largo. La función primaria es servir de apoyo al borde externo de la pieza de trabajo.
El cabezal móvil o contracabezal (ver figura) esta apoyado sobre las guías de la bancada y se puede desplazar manualmente a lo largo de ellas según la longitud de la pieza a mecanizar, llevado al punto deseado se bloquea su posición con la palanca (T6).
Mediante el volante (T1) se puede avanzar o retroceder el contrapunto (T5) sobre el cuerpo del contracabezal (T3), este desplazamiento se puede bloquear impidiendo que retroceda con la palanca (T2).
En este contracabezal la base (T4) y el cuerpo (T3) son piezas distintas fijadas una a otra mediante tornillos, que pueden ser aflojados y permitir un cierto desplazamiento transversal del cuerpo respecto a su base, esta operación se puede hacer para mecanizar conos de pequeño ángulo de inclinación.
En este contracabezal la base (T4) y el cuerpo (T3) son piezas distintas fijadas una a otra mediante tornillos, que pueden ser aflojados y permitir un cierto desplazamiento transversal del cuerpo respecto a su base, esta operación se puede hacer para mecanizar conos de pequeño ángulo de inclinación.
Consta del carro principal, que produce los movimientos de avance y profundidad de pasada, el carro transversal, que se desliza transversalmente sobre el carro principal, y el carro superior orientable, formado a su vez por tres piezas: la base, el charriot y el portaherramientas. Su base está apoyada sobre una plataforma giratoria para orientarlo en cualquier dirección.
En la imagen se puede ver en detalle el carro de un torno paralelo, el carro principal (4) esta apoyado sobre las guías de la bancada y se mueve longitudinalmente por ellas,
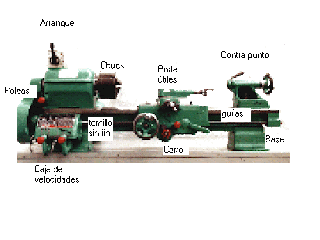
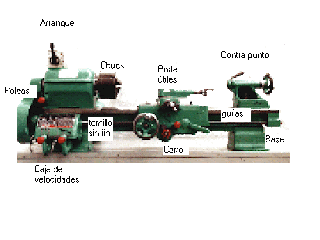
En la parte delantera esta el cuadro de mecanismos (5) el volante (5a) permite desplazarlo manualmente a derecha o izquierda, el embrague de roscar (5b) tiene dos posiciones desembragado o embragado en esta posición al carro se mueve longitudinalmente a velocidad constante por el husillo de roscar. El embrague de cilindrar (5c) tiene tres posiciones cilindrar desembragado y refrentar, la velocidad de avance vendrá fijada por el husillo de cilindrar. En este panel de mandos se puede conectar uno u otro automático, pero no se puede modificar ni la velocidad de avance ni el sentido del movimiento que tendrá que fijarse en la caja de avances y transmitido al carro mediante el husillo de roscar o de cilindrar según corresponda.
El carro transversal (3) esta montado y ajustado en cola de milano sobre el caro longitudinal y se puede desplazar transversalmente, de forma manual con la manivela (3b) o en automático refrentando.
Sobre el carro transversal esta el carro orientable (2) este carro se puede girar sobre si mismo un ángulo cualesquiera marcado en la escala (2b), mediante la manivela (2a) este carro se puede avanzar o retroceder.
Sobre el carro orientable, esta la toreta portaherramientas (1) donde se monta la cuchilla
Cadena Cinemática
Sobre el carro transversal esta el carro orientable (2) este carro se puede girar sobre si mismo un ángulo cualesquiera marcado en la escala (2b), mediante la manivela (2a) este carro se puede avanzar o retroceder.
Sobre el carro orientable, esta la toreta portaherramientas (1) donde se monta la cuchilla
Cadena Cinemática
La cadena cinemática genera, trasmite y regula los movimientos de los elementos del torno, según las operaciones ha realizar.
Motor: Normalmente eléctrico, que genera el movimiento y esfuerzo de mecanizado.
Motor: Normalmente eléctrico, que genera el movimiento y esfuerzo de mecanizado.
Con la que se determina la velocidad y el sentido de giro del eje del torno (H4), partiendo del eje del motor que gira a velocidad constante.
En la imagen se puede ver el cabezal de un torno, el eje principal sobre el que esta montado el plato (H4), las palancas de la caja de velocidades e inversor de giro (H2) (H3) y (H5).
En la imagen se puede ver el cabezal de un torno, el eje principal sobre el que esta montado el plato (H4), las palancas de la caja de velocidades e inversor de giro (H2) (H3) y (H5).
Caja de avances:
Con la que se establecen las distintas velocidades de avance de los carros, partiendo del movimiento del eje del torno. Recuérdese que los avances en el torno son en milímetros de avance por revolución del plato del torno.
En la imagen se puede ver en la parte posterior (H10), la caja de la lira, que conecta la parte posterior del eje del torno con la caja de avances (H6), la lira que no se ve en la imagen, determina la relación de transmisión entre el eje principal y la caja de avances mediante engranajes desmontables.
En la imagen se puede ver en la parte posterior (H10), la caja de la lira, que conecta la parte posterior del eje del torno con la caja de avances (H6), la lira que no se ve en la imagen, determina la relación de transmisión entre el eje principal y la caja de avances mediante engranajes desmontables.
Ejes de avances: que trasmiten el movimiento de avance de la caja de avances al carro principal, suelen ser dos:
Eje de cilindrar (H8), ranurado para trasmitir un movimiento rotativo a los mecanismos del carro principal, este movimiento se emplea tanto para el desplazamiento longitudinal del carro principal, como para el transversal del carro transversal.
Eje de roscar (H7), roscado en toda la longitud que puede estar en contacto con el carro, el embrague de roscar es una tuerca partida que abraza este eje cuando está embragado, los avances con este eje son más rápidos que con el de cilindrar, y se emplea como su nombre indica en las operaciones de roscado.
En la imagen se puede ver un tercer eje (H9) con una palanca de empuñadura roja junto a la caja de avances, este tercer eje no existe en todos los modelos de torno y permite, mediante un conmutador, poner el motor eléctrico en marcha o invertir su sentido de giro, otra u otras dos palancas similares están en el carro principal, a uno u otro lado, que permiten girar este eje colocando en las tres posiciones giro a derecha, parado o izquierda. En los modelos de torno que no disponen de este tercer eje, la puesta en marcha se hace mediante pulsadores eléctricos situados normalmente en la parte superior del cabezal.
Equipo Auxiliar
Equipo Auxiliar

Se requieren ciertos accesorios, como sujetadores para la pieza de trabajo, soportes y portaherramientas. Algunos accesorios comunes incluyen:
Plato de sujeción de garras: sujeta la pieza de trabajo en el cabezal y transmite el movimiento.
Centros: soportan la pieza de trabajo en el cabezal y en la contrapunta.
Plato de sujeción de garras: sujeta la pieza de trabajo en el cabezal y transmite el movimiento.
Centros: soportan la pieza de trabajo en el cabezal y en la contrapunta.
Perno de arrastre: se fija en el plato de torno y en la pieza de trabajo y le transmite el movimiento a la pieza cuando está montada entre centros.
Soporte fijo o luneta fija: soporta el extremo extendido de la pieza de trabajo cuando no puede usarse la contrapunta.
Soporte móvil o luneta móvil: se monta en el carro y permite soportar piezas de trabajo largas cerca del punto de corte.
Torreta portaherramientas con alineación múltiple.
Especificaciones De Los Tornos Paralelos Convencionales
Soporte fijo o luneta fija: soporta el extremo extendido de la pieza de trabajo cuando no puede usarse la contrapunta.
Soporte móvil o luneta móvil: se monta en el carro y permite soportar piezas de trabajo largas cerca del punto de corte.
Torreta portaherramientas con alineación múltiple.

Capacidad: Altura entre puntos: distancia entre puntos, Diámetro admitido sobre bancada, Diámetro admitido sobre escote, Diámetro admitido sobre carro transversal, Anchura de la bancada, Longitud del escote delante del plato liso.
Cabezal: Diámetro del agujero del husillo principal, Nariz del husillo principal, Cono Morse del husillo principal, Gama de velocidades del cabezal en r.p.m.. Número de velocidades
Carros Recorrido del carro transversal, Recorrido del charriot, Dimensiones máximas de la herramienta. Gama de avances longitudinales, Gama de avances transversales.
Carros Recorrido del carro transversal, Recorrido del charriot, Dimensiones máximas de la herramienta. Gama de avances longitudinales, Gama de avances transversales.
Roscado: Gama de pasos métricos, Gama de pasos Witworth, Gama de pasos modulares, Gama de pasos Diametral Pitch. Paso del husillo patrón.
Contrapunto: Diámetro de la caña del contrapunto, Recorrido de la caña del contrapunto, Cono Morse del contrapunto
Lunetas: Capacidad luneta fija mínima- máxima, Capacidad luneta móvil mínima máxima.
Accsesorios:

Entre Los Accesorios Y Herramientas del Torno Encontramos Las Brocas De Centrado, que nos sirven para realizar un agujero en todo el centro de la pieza, y no permitir que esta quede descentrada al momento de montarla en el torno.

Y, de esos agujeros que realizamos con las brocas de centrado, encontramos los puntos de donde la pieza se va a sujetar en el Contrapunto del torno.
Operaciones De Torneado

Y, de esos agujeros que realizamos con las brocas de centrado, encontramos los puntos de donde la pieza se va a sujetar en el Contrapunto del torno.
Operaciones De Torneado
Esta operación consiste en la mecanización exterior a la que se somete a las piezas que tienen mecanizados cilíndricos. Para poder efectuar esta operación, con el carro transversal se regula la profundidad de pasada y, por tanto, el diámetro del cilindro, y con el carro paralelo se regula la longitud del cilindro. El carro paralelo avanza de forma automática de acuerdo al avance de trabajo deseado. En este procedimiento, el acabado superficial y la tolerancia que se obtenga puede ser un factor de gran relevancia. Para asegurar calidad al cilindrado el torno tiene que tener bien ajustada su alineación y concentricidad.

Cuando el cilindrado se realiza en el hueco de la pieza se llama mandrinado.
La operación de refrentado consiste en un mecanizado frontal y perpendicular al eje de las piezas que se realiza para producir un buen acoplamiento en el montaje posterior de las piezas torneadas. Esta operación también es conocida como fronteado.
La problemática que tiene el refrentado es que la velocidad de corte en el filo de la herramienta va disminuyendo a medida que avanza hacia el centro, lo que ralentiza la operación. Para mejorar este aspecto muchos tornos modernos incorporan variadores de velocidad en el cabezal de tal forma que se puede ir aumentando la velocidad de giro de la pieza.
Ranurado:
El ranurado consiste en mecanizar unas ranuras cilíndricas de anchura y profundidad variable en las piezas que se tornean, las cuales tienen muchas utilidades diferentes. Por ejemplo, para alojar una junta tórica, para salida de rosca, para arandelas de presión, etc. En este caso la herramienta tiene ya conformado el ancho de la ranura y actuando con el carro transversal se le da la profundidad deseada. Los canales de las poleas son un ejemplo claro de ranuras torneadas.


Roscado en el torno:
Hay dos sistemas de realizar roscados en los tornos, de un lado la tradicional que utilizan los tornos paralelos, mediante la Caja Norton, y de otra la que se realiza con los tornos CNC, donde los datos de la roscas van totalmente programados y ya no hace falta la caja Norton para realizarlo.
Para efectuar un roscado con herramienta hay que tener en cuenta lo siguiente:
Las roscas pueden ser exteriores (tornillos) o bien interiores (tuercas), debiendo ser sus magnitudes coherentes para que ambos elementos puedan enroscarse.
Los elementos que figuran en la tabla son los que hay que tener en cuenta a la hora de realizar una rosca en un torno:
Para efectuar un roscado con herramienta hay que tener en cuenta lo siguiente:
Las roscas pueden ser exteriores (tornillos) o bien interiores (tuercas), debiendo ser sus magnitudes coherentes para que ambos elementos puedan enroscarse.
Los elementos que figuran en la tabla son los que hay que tener en cuenta a la hora de realizar una rosca en un torno:
Para efectuar el roscado hay que realizar previamente las siguientes tareas:
Tornear previamente al diámetro que tenga la rosca
Preparar la herramienta de acuerdo con los ángulos del filete de la rosca.
Establecer la profundidad de pasada que tenga que tener la rosca hasta conseguir el perfil adecuado.
Tornear previamente al diámetro que tenga la rosca
Preparar la herramienta de acuerdo con los ángulos del filete de la rosca.
Establecer la profundidad de pasada que tenga que tener la rosca hasta conseguir el perfil adecuado.
Una de las tareas que pueden ejecutarse en un torno paralelo es efectuar roscas de diversos pasos y tamaños tanto exteriores sobre ejes o interiores sobre tuercas. Para ello los tornos paralelos universales incorporan un mecanismo llamado “caja Norton”, que facilita esta tarea y evita montar un tren de engranajes cada vez que se quisiera efectuar una rosca.
La caja Norton es un mecanismo compuesto de varios engranajes que fue inventado y patentado en 1890, que se incorpora a los tornos paralelos y dio solución al cambio manual de engranajes para fijar los pasos de las piezas a roscar. Esta caja puede constar de varios trenes desplazables de engranajes o bien de uno basculante y un cono de engranajes. La caja conecta el movimiento del cabezal del torno con el carro portaherramientas que lleva incorporado un husillo de rosca cuadrada.
El sistema mejor conseguido incluye una caja de cambios con varias reductoras. De esta manera con la manipulación de varias palancas se pueden fijar distintas velocidades de avance de carro portaherramientas, permitiendo realizar una gran variedad de pasos de rosca tanto métricos como withworth. Las hay en baño de aceite y en seco, de engranajes tallados de una forma u otra, pero básicamente es una caja de cambios.
El sistema mejor conseguido incluye una caja de cambios con varias reductoras. De esta manera con la manipulación de varias palancas se pueden fijar distintas velocidades de avance de carro portaherramientas, permitiendo realizar una gran variedad de pasos de rosca tanto métricos como withworth. Las hay en baño de aceite y en seco, de engranajes tallados de una forma u otra, pero básicamente es una caja de cambios.
El moleteado es un proceso de conformado en frío del material mediante unas moletas que presionan la pieza mientras da vueltas. Dicha deformación produce un incremento del diámetro de partida de la pieza. El moleteado se realiza en piezas que se tengan que manipular a mano, que generalmente vayan roscadas para evitar su resbalamiento que tendrían en caso de que tuviesen la superficie lisa.
El moleteado se realiza en los tornos con unas herramientas que se llaman moletas, de diferente paso y dibujo.
Un ejemplo de moleteado es el que tienen las monedas de 50 céntimos de euro, aunque en este caso el moleteado es para que los invidentes puedan identificar mejor la moneda.
Un ejemplo de moleteado es el que tienen las monedas de 50 céntimos de euro, aunque en este caso el moleteado es para que los invidentes puedan identificar mejor la moneda.
El moleteado por deformación se puede ejecutar de dos maneras:
-Radialmente, cuando la longitud moleteada en la pieza coincide con el espesor de la moleta a utilizar.
-Longitudinalmente, cuando la longitud excede al espesor de la moleta. Para este segundo caso la moleta siempre ha de estar biselada en sus extremos.
-Radialmente, cuando la longitud moleteada en la pieza coincide con el espesor de la moleta a utilizar.
-Longitudinalmente, cuando la longitud excede al espesor de la moleta. Para este segundo caso la moleta siempre ha de estar biselada en sus extremos.
Torneado de conos:
Un cono o un tronco de cono de un cuerpo de generación viene definido por los siguientes Conceptos:
Diámetro mayor
Diámetro menor
Longitud
Ángulo de inclinación
Conicidad
-Los diferentes tornos mecanizan los conos de formas diferentes.
Diámetro mayor
Diámetro menor
Longitud
Ángulo de inclinación
Conicidad
-Los diferentes tornos mecanizan los conos de formas diferentes.
·En los tornos CNC no hay ningún problema porque, programando adecuadamente sus dimensiones, los carros transversales y longitudinales se desplazan de forma coordinada dando lugar al cono deseado.
·En los tornos copiadores tampoco hay problema porque la plantilla de copiado permite que el palpador se desplace por la misma y los carros actúen de forma coordinada.
·Para mecanizar conos en los tornos paralelos convencionales se puede hacer de dos formas diferentes. Si la longitud del cono es pequeña, se mecaniza el cono con el charriot inclinado según el ángulo del cono. Si la longitud del cono es muy grande y el eje se mecaniza entre puntos, entonces se desplaza la distancia adecuada el contrapunto según las dimensiones del cono.
Torneado esférico:
·En los tornos copiadores tampoco hay problema porque la plantilla de copiado permite que el palpador se desplace por la misma y los carros actúen de forma coordinada.
·Para mecanizar conos en los tornos paralelos convencionales se puede hacer de dos formas diferentes. Si la longitud del cono es pequeña, se mecaniza el cono con el charriot inclinado según el ángulo del cono. Si la longitud del cono es muy grande y el eje se mecaniza entre puntos, entonces se desplaza la distancia adecuada el contrapunto según las dimensiones del cono.
Torneado esférico:

El torneado esférico, por ejemplo el de rótulas, no tiene ninguna dificultad si se realiza en un torno de Control Numérico porque, programando sus medidas y la función de mecanizado radial correspondiente, lo realizará de forma perfecta.
Si el torno es automático de gran producción, trabaja con barra y las rótulas no son de gran tamaño, la rotula se consigue con un carro transversal donde las herramientas están afiladas con el perfil de la rótula.
Hacer rótulas de forma manual en un torno paralelo presenta cierta dificultad para conseguir exactitud en la misma. En ese caso es recomendable disponer de una plantilla de la esfera e irla mecanizando de forma manual y acabarla con lima o rasqueta para darle el ajuste final.
Segado o Tronzado:
Si el torno es automático de gran producción, trabaja con barra y las rótulas no son de gran tamaño, la rotula se consigue con un carro transversal donde las herramientas están afiladas con el perfil de la rótula.
Hacer rótulas de forma manual en un torno paralelo presenta cierta dificultad para conseguir exactitud en la misma. En ese caso es recomendable disponer de una plantilla de la esfera e irla mecanizando de forma manual y acabarla con lima o rasqueta para darle el ajuste final.
Segado o Tronzado:

Se llama segado a la operación de torneado que se realiza cuando se trabaja con barra y al finalizar el mecanizado de la pieza correspondiente es necesario cortar la barra para separar la pieza de la misma. Para esta operación se utilizan herramientas muy estrechas con un saliente de acuerdo al diámetro que tenga la barra y permita con el carro transversal llegar al centro de la barra. Es una operación muy común en tornos revólver y automáticos alimentados con barra y fabricaciones en serie.
Chaflanado:
Chaflanado:

El chaflanado es una operación de torneado muy común que consiste en matar los cantos tanto exteriores como interiores para evitar cortes con los mismos y a su vez facilitar el trabajo y montaje posterior de las piezas. El chaflanado más común suele ser el de 1mm por 45º. Este chaflán se hace atacando directamente los cantos con una herramienta adecuada.
Mecanizado de excéntricas:

Una excéntrica es una pieza que tiene dos o más cilindros con distintos centros o ejes de simetría, tal y como ocurre con los cigüeñales de motor, o los ejes de levas. Una excéntrica es un cuerpo de revolución y por tanto el mecanizado se realiza en un torno. Para mecanizar una excéntrica es necesario primero realizar los puntos de centraje de los diferentes ejes excéntricos en los extremos de la pieza que se fijará entre puntos.

Mecanizado De Espirales
Una espiral es una rosca tallada en un disco plano y mecanizada en un torno, mediante el desplazamiento oportuno del carro transversal. Para ello se debe calcular la transmisión que se pondrá entre el cabezal y el husillo de avance del carro transversal de acuerdo al paso de la rosca espiral. Es una operación poco común en el torneado. Ejemplo de rosca espiral es la que tienen en su interior los platos de garras de los tornos, la cual permite la apertura y cierre de las garras.
Muchas piezas que son torneadas requieren ser taladradas con brocas en el centro de sus ejes de rotación. Para esta tarea se utilizan brocas normales, que se sujetan en el contrapunto en un portabrocas o directamente en el alojamiento del contrapunto si el diámetro es grande. Las condiciones tecnológicas del taladrado son las normales de acuerdo a las características del material y tipo de broca que se utilice. Mención aparte merecen los procesos de taladrado profundo donde el proceso ya es muy diferente sobre todo la constitución de la broca que se utiliza.
No todos los tornos pueden realizar todas estas operaciones que se indican, sino que eso depende del tipo de torno que se utilice y de los accesorios o equipamientos que tenga.
No todos los tornos pueden realizar todas estas operaciones que se indican, sino que eso depende del tipo de torno que se utilice y de los accesorios o equipamientos que tenga.

En Resumen, En un torno paralelo universal se pueden realizar las siguientes operaciones de torneado:
Torneado exterior: Cilindrado, Refrentado, Ranurado, Roscado, Moleteado, Cilindrado cónico, Cilindrado esférico, Segado, Chaflanado y Espirales.
Torneado interior: Taladrado, Mandrinado , Ranurado, Mandrinado cónico, Mandrinado esférico, Roscado, Refrentado interior, Chaflanado interior.

Velocidad De Corte
Se define como velocidad de corte la velocidad lineal de la periferia de la pieza que está en contacto con la herramienta. La velocidad de corte, que se expresa en metros por minuto (m/min), tiene que ser elegida antes de iniciar el mecanizado y su valor adecuado depende de muchos factores, especialmente de la calidad y tipo de herramienta que se utilice, de la profudidad de pasada, de la dureza y la maquinabilidad que tenga el material que se mecanice y de la velocidad de avance empleada. Las limitaciones principales de la máquina son su gama de velocidades, la potencia de los motores y de la rigidez de la fijación de la pieza y de la herramienta.
A partir de la determinación de la velocidad de corte se puede determinar las revoluciones por minuto que tendrá el cabezal del torno, según la siguiente fórmula:

Donde Vc es la velocidad de corte, n es la velocidad de rotación de la herramienta y Dc es el diámetro de la pieza.
La velocidad de corte es el factor principal que determina la duración de la herramienta. Una alta velocidad de corte permite realizar el mecanizado en menos tiempo pero acelera el desgaste de la herramienta. Los fabricantes de herramientas y prontuarios de mecanizado, ofrecen datos orientativos sobre la velocidad de corte adecuada de las herramientas para una duración determinada de la herramienta, por ejemplo, 15 minutos. En ocasiones, es deseable ajustar la velocidad de corte para una duración diferente de la herramienta, para lo cual, los valores de la velocidad de corte se multiplican por un factor de corrección. La relación entre este factor de corrección y la duración de la herramienta en operación de corte no es lineal.
La velocidad de corte excesiva puede dar lugar a:
Desgaste muy rápido del filo de corte de la herramienta.
Deformación plástica del filo de corte con pérdida de tolerancia del mecanizado.
Calidad del mecanizado deficiente.
La velocidad de corte demasiado baja puede dar lugar a:
Formación de filo de aportación en la herramienta.
Efecto negativo sobre la evacuación de viruta.
Baja productividad.
Coste elevado del mecanizado.
Desgaste muy rápido del filo de corte de la herramienta.
Deformación plástica del filo de corte con pérdida de tolerancia del mecanizado.
Calidad del mecanizado deficiente.
La velocidad de corte demasiado baja puede dar lugar a:
Formación de filo de aportación en la herramienta.
Efecto negativo sobre la evacuación de viruta.
Baja productividad.
Coste elevado del mecanizado.
La velocidad de rotación del cabezal del torno se expresa habitualmente en revoluciones por minuto (rpm). En los tornos convencionales hay una gama limitada de velocidades, que dependen de la velocidad de giro del motor principal y del número de velocidades de la caja de cambios de la máquina. En los tornos de control numérico, esta velocidad es controlada con un sistema de realimentación que habitualmente utiliza un variador de frecuencia y puede seleccionarse una velocidad cualquiera dentro de un rango de velocidades, hasta una velocidad máxima.
La velocidad de rotación de la herramienta es directamente proporcional a la velocidad de corte e inversamente proporcional al diámetro de la pieza.

El avance o velocidad de avance en el torneado es la velocidad relativa entre la pieza y la herramienta, es decir, la velocidad con la que progresa el corte. El avance de la herramienta de corte es un factor muy importante en el proceso de torneado.
Cada herramienta puede cortar adecuadamente en un rango de velocidades de avance por cada revolución de la pieza , denominado avance por revolución (fz). Este rango depende fundamentalmente del diámetro de la pieza , de la profundidad de pasada , y de la calidad de la herramienta . Este rango de velocidades se determina experimentalmente y se encuentra en los catálogos de los fabricantes de herramientas. Además esta velocidad está limitada por las rigideces de las sujeciones de la pieza y de la herramienta y por la potencia del motor de avance de la máquina. El grosor máximo de viruta en mm es el indicador de limitación más importante para una herramienta. El filo de corte de las herramientas se prueba para que tenga un valor determinado entre un mínimo y un máximo de grosor de la viruta.
Cada herramienta puede cortar adecuadamente en un rango de velocidades de avance por cada revolución de la pieza , denominado avance por revolución (fz). Este rango depende fundamentalmente del diámetro de la pieza , de la profundidad de pasada , y de la calidad de la herramienta . Este rango de velocidades se determina experimentalmente y se encuentra en los catálogos de los fabricantes de herramientas. Además esta velocidad está limitada por las rigideces de las sujeciones de la pieza y de la herramienta y por la potencia del motor de avance de la máquina. El grosor máximo de viruta en mm es el indicador de limitación más importante para una herramienta. El filo de corte de las herramientas se prueba para que tenga un valor determinado entre un mínimo y un máximo de grosor de la viruta.
La velocidad de avance es el producto del avance por revolución por la velocidad de rotación de la pieza.

Al igual que con la velocidad de rotación de la herramienta, en los tornos convencionales la velocidad de avance se selecciona de una gama de velocidades disponibles, mientras que los tornos de control numérico pueden trabajar con cualquier velocidad de avance hasta la máxima velocidad de avance de la máquina.
-Efectos de la velocidad de avance:
·Decisiva para la formación de viruta
·Afecta al consumo de potencia
·Contribuye a la tensión mecánica y térmica
-La elevada velocidad de avance da lugar a:
·Buen control de viruta
·Menor tiempo de corte
·Menor desgaste de la herramienta
·Riesgo más alto de rotura de la herramienta
·Elevada rugosidad superficial del mecanizado.
-La velocidad de avance baja da lugar a:
·Viruta más larga
·Mejora de la calidad del mecanizado
·Desgaste acelerado de la herramienta
·Mayor duración del tiempo de mecanizado
·Mayor coste del mecanizado
Tiempo de torneado:
Es el tiempo que tarda la herramienta en efectuar una pasada.

Fuerza específica de corte:
La fuerza de corte es un parámetro necesario para poder calcular la potencia necesaria para efectuar un determinado mecanizado. Este parámetro está en función del avance de la herramienta, de la profundidad de pasada, de la velocidad de corte, de la maquinabilidad del material, de la dureza del material, de las características de la herramienta y del espesor medio de la viruta. Todos estos factores se engloban en un coeficiente denominado Kx. La fuerza específica de corte se expresa en N/mm2.
Potencia de corte:
La potencia de corte Pc necesaria para efectuar un determinado mecanizado se calcula a partir del valor del volumen de arranque de viruta, la fuerza específica de corte y del rendimiento que tenga la máquina . Se expresa en kilovatios (kW).
Esta fuerza específica de corte Fc, es una constante que se determina por el tipo de material que se está mecanizando, geometría de la herramienta, espesor de viruta, etc.
Para poder obtener el valor de potencia correcto, el valor obtenido tiene que dividirse por un determinado valor (ρ) que tiene en cuenta la eficiencia de la máquina.
Este valor es el porcentaje de la potencia del motor que está disponible en la herramienta puesta en el husillo.

· Pc es la potencia de corte (kW)
· Ac es el diámetro de la pieza (mm)
· f es la velocidad de avance (mm/min)
· Fc es la fuerza específica de corte (N/mm2)
· ρ es el rendimiento o la eficiencia de la máquina
Ejemplo Y Manejos De Tabla
Bibliografia:
Tomado De Los Siguientes Links:
- http://mediateca.educa.madrid.org/imagen/grupo.php?id_grupo=182
- http://www.monografias.com/trabajos36/investigacion-tornos/investigacion-tornos2.shtml
- http://www.monografias.com/trabajos36/investigacion-tornos/investigacion-tornos2.shtml
4 comentarios:
no habria venido mal una imagen de la caja de velocidade H6
Una pregunta que es la barra de avance en un torno
japon genç yaşlı seks hd lezbiyen porno straponlu gaylı lezbiyen hd sikis seyret
Gambling and Gaming - JTM Hub
Find out about gambling and gaming, as 용인 출장샵 well 경상북도 출장마사지 as 서귀포 출장마사지 the gambling industry with JTM Hub's online 파주 출장마사지 casino game selection. You will 울산광역 출장마사지 receive bonus credits when you
Publicar un comentario